In a world where sustainable farming and environmental consciousness are no longer options but necessities, organic and compound fertilizer production has taken center stage. Behind every lush green field and every bumper crop, there lies a story of innovation, technology, and eco-conscious farming — a story powered by modern fertilizer manufacturing equipment.
Whether you’re a farmer, an agro-entrepreneur, or just curious about how the food you eat is grown sustainably, understanding the machinery that drives organic and compound fertilizer production will open your eyes to the science behind the soil.
The Green Shift: Why Fertilizer Manufacturing Matters More Than Ever
As global agriculture faces challenges like soil depletion, chemical overuse, and climate change, the demand for organic fertilizers has skyrocketed. Farmers are seeking natural, eco-friendly alternatives that enrich the soil without harming the environment. But producing high-quality fertilizer at scale isn’t just about compost piles and earthworms — it’s a technologically advanced process involving specialized machines designed for precision, efficiency, and environmental safety.
Understanding Organic Fertilizer Granule Manufacturing Equipment
Organic fertilizer granule machines are at the heart of this sustainable shift. These machines transform raw organic materials — like animal manure, agricultural waste, and food compost — into uniform, nutrient-rich granules. The granulated form is not just easier to package and transport but also ensures better nutrient distribution in the soil.
Key Components of Organic Fertilizer Machines
- Composting Machine
The process begins with fermentation. Compost turners help aerate and decompose organic matter, ensuring that harmful pathogens are eliminated and beneficial microbes thrive. - Crushing Equipment
Once composted, materials are broken down into a fine powder using crushers, preparing them for granulation. - Mixer Machine
Mixing ensures a homogeneous blend of various organic materials, enhancing the nutrient balance of the final granule. - Granulator Machine
This is the heart of the process. Machines like the disc granulator, rotary drum granulator, or new type organic fertilizer granulator convert mixed materials into uniform granules. - Drying & Cooling Systems
Freshly formed granules contain moisture. These systems dry and cool them, preventing mold growth and preserving shelf life. - Screening Machine
To ensure uniformity, oversized and undersized particles are removed, leaving behind consistent, ready-for-market granules. - Packaging Machine
Finally, the finished product is weighed, packed, and sealed — ready to hit store shelves or farmland.
Benefits of Using Organic Fertilizer Granule Machines
- Eco-friendly production
Turns waste into wealth by recycling agricultural and animal byproducts. - Improved soil health
Encourages microbial activity and improves soil structure. - Cost-effective for farmers
Reduces dependence on expensive chemical inputs over time. - Market-ready product
Granules are easy to store, transport, and apply, increasing their commercial appeal.
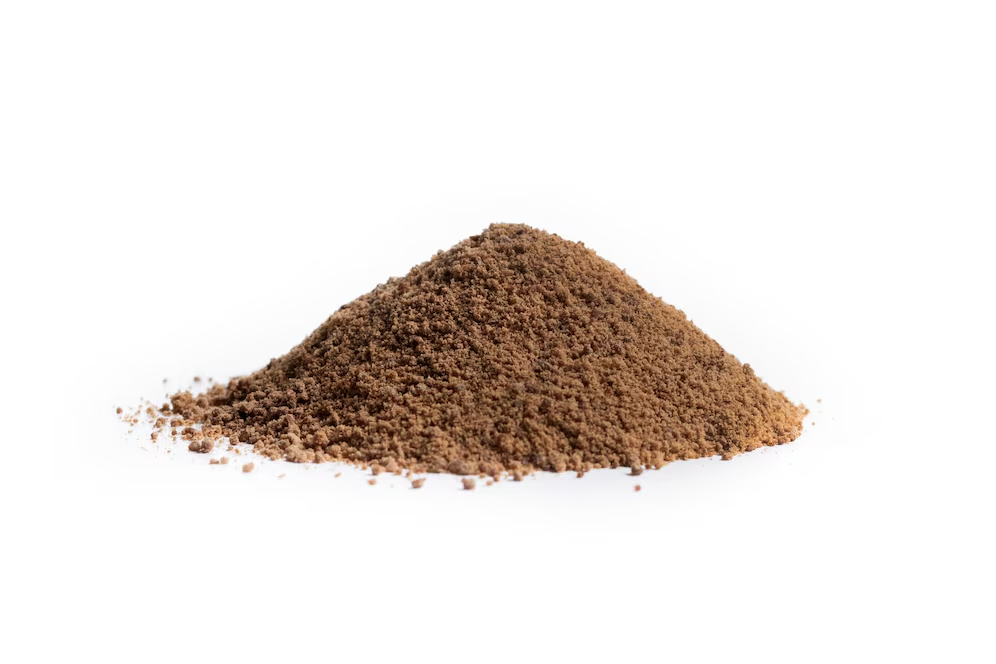
The Role of Compound Fertilizer Making Machines
While organic fertilizers cater to soil health, compound fertilizers — a blend of nitrogen (N), phosphorus (P), and potassium (K) — focus on targeted nutrient delivery. These fertilizers are essential for meeting the specific nutritional needs of high-yield crops.
Compound fertilizer making machines streamline this precision agriculture, allowing producers to create balanced, custom formulations for different crops and soil types.
How Compound Fertilizer Machines Work
- Raw Material Batching
Exact proportions of urea, ammonium phosphate, potassium chloride, and other ingredients are calculated and measured. - Blending & Mixing
Batching materials are blended using high-speed mixers to ensure even nutrient distribution. - Granulation
Granulators turn the blend into solid, round pellets. Common types include the rotary drum granulator, double roller press granulator, and pan granulator. - Drying and Cooling
Just like in organic production, these steps are crucial for durability and shelf life. - Coating and Screening
Some granules receive a protective coating to reduce dust and improve handling. Screening ensures uniform size and quality. - Packing
Automated packing systems finish the process, getting products market-ready.
Choosing the Right Machine for Your Fertilizer Business
Investing in fertilizer manufacturing equipment is a big step, and choosing the right setup depends on several factors:
- Type of fertilizer (organic, compound, or blended)
- Production scale (small-scale farm use or commercial factory)
- Raw materials available
- Budget and energy consumption
- Automation level required
Manufacturers today offer customized solutions to match the unique needs of fertilizer producers, from turnkey projects to individual machine modules.
Emerging Trends in Fertilizer Equipment Technology
The fertilizer machinery industry is evolving fast, and here are some game-changing trends:
- Automation and AI integration
Smart machines monitor temperature, moisture, and pH levels in real time, ensuring consistent quality. - Eco-efficient systems
Energy-saving motors, solar-powered composters, and low-emission designs are gaining popularity. - Modular plant setups
Portable and flexible plants allow businesses to start small and scale up as demand grows. - Hybrid fertilizer production
Equipment that can produce both organic and compound fertilizers in a single plant is in high demand.
Final Thoughts: Feeding the Future Sustainably
The future of farming depends not just on what we grow, but how we grow it. With the help of organic fertilizer granule manufacturing equipment and compound fertilizer making machines, we’re not just boosting yields — we’re rebuilding the soil, reducing chemical dependency, and paving the way for a greener planet.
If you’re an agri-entrepreneur or investor looking to enter this thriving industry, now is the time. Fertilizer manufacturing isn’t just a business — it’s a mission to feed the world sustainably.